Custom plastic extrusion tailored to your industry needs
Custom plastic extrusion tailored to your industry needs
Blog Article
Checking Out the Different Methods and Technologies Behind Plastic Extrusion
The world of plastic extrusion is a blend of precision, technology, and technology, essential to numerous industries worldwide. Advanced equipment, digital controls, and a selection of materials converge in this intricate procedure, generating top quality, long lasting items.
Comprehending the Fundamentals of Plastic Extrusion
The process of plastic extrusion, usually hailed as a foundation in the world of manufacturing, forms the bedrock of this discussion. In essence, plastic extrusion is a high-volume manufacturing procedure in which raw plastic material is thawed and formed into a continuous account. It's an approach commonly utilized for developing products with a continuous cross-sectional account, such as pipes, window structures, and climate removing. The process begins with feeding plastic products, frequently in the type of pellets, into a warmed barrel. There, it is heated and blended until it ends up being molten. The liquified plastic is after that compelled via a die, shaping it into the desired type as it solidifies and cools.
The Function of Different Materials in Plastic Extrusion
While plastic extrusion is a typically utilized technique in production, the products made use of in this process significantly influence its final output. Different kinds of plastics, such as polyethylene, PVC, and abdominal muscle, each provide one-of-a-kind buildings throughout item. Polyethylene, recognized for its durability and adaptability, is often utilized in packaging, while PVC, renowned for its strength and resistance to ecological factors, is used in building. ABS, on the various other hand, combines the very best characteristics of both, resulting in high-impact resistance and toughness. The selection of material not just affects the item's physical homes but also affects the extrusion rate and temperature. Consequently, manufacturers must thoroughly consider the buildings of the material to maximize the extrusion process.
Methods Made Use Of in the Plastic Extrusion Refine
The plastic extrusion procedure entails numerous strategies that are crucial to its operation and efficiency (plastic extrusion). The conversation will begin with a simplified explanation of the basics of plastic extrusion. This will be followed by a breakdown of the process thoroughly and an exploration of methods to enhance the efficiency of the extrusion technique
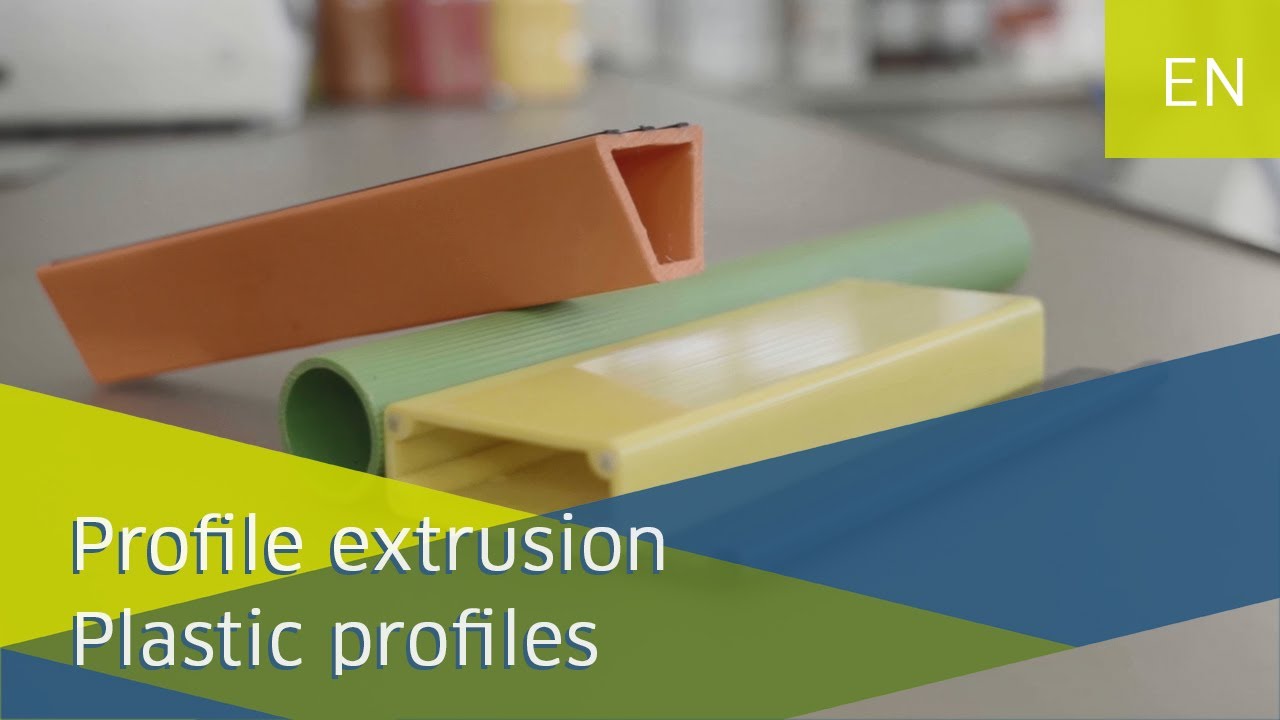
Recognizing Plastic Extrusion Fundamentals
In the world of manufacturing, plastic extrusion stands as an essential procedure, important in the production of a plethora of everyday items. At its core, plastic extrusion includes changing raw plastic product into a constant profiled form. This is achieved by melting the plastic, frequently in the kind of pellets or granules, and requiring it via a designed die. The resulting item is a long plastic piece, such as a pipeline, panel, or cable layer, that maintains the shape of the die. This affordable approach is extremely functional, able to develop complex forms and accommodate a wide array of plastic products. Basic understanding of these essentials enables further expedition of the extra detailed facets of plastic extrusion.
In-depth Extrusion Process Break Down

Improving Extrusion Strategy Efficiency
Efficiency gains in the plastic extrusion process can substantially impact both the top quality of the final product and the general efficiency of the operation. Continual optimization of the extrusion method is essential to preserving an affordable side. Regular maintenance of extrusion devices can additionally reduce downtimes, hence raising performance.
Just How Innovation Is Altering the Face of Plastic Extrusion
The advent of brand-new innovation has dramatically transformed the landscape of plastic extrusion. It has brought about the advancement of sophisticated extrusion equipment, which has boosted the performance and high quality of the plastic extrusion process. Moreover, innovations in the extrusion procedure have likewise been driven by technical developments, providing enhanced capacities and adaptability.
Advanced Extrusion Machinery
Revolutionizing the world of plastic extrusion, progressed equipment imbued with advanced technology is introducing a brand-new period of efficiency and precision. These machines, outfitted with ingenious features like automatic temperature control systems, ensure ideal problems for plastic handling, consequently lessening waste and enhancing product top quality. High-speed extruders, for circumstances, amplify output rates, while twin-screw extruders offer superior blending capabilities, important for producing complicated plastic blends. In addition, digital control systems provide extraordinary accuracy in procedures, minimizing human error. These devices are made for longevity, reducing downtime and upkeep costs. While these innovations are already exceptional, the continuous development of modern technology promises even better leaps forward in the area of plastic extrusion equipment.
Advancements in Extrusion Procedures
Utilizing the power of modern innovation, plastic extrusion processes are going through a transformative metamorphosis. With the advent of 3D printing, the plastic extrusion landscape is additionally broadening into brand-new realms of opportunity. These technological breakthroughs are not just improving the top quality of extruded plastic products yet likewise propelling the sector towards an extra sustainable, reliable, and innovative future.
Real-World Applications of Plastic Extrusion
Plastic extrusion, a versatile and effective procedure, finds use in countless real-world applications. It's mostly employed in the production market, where it's made use of to create a myriad of items such as pipelines, tubes, home window frames, climate removing, and secure fencing. The automotive industry also uses this modern technology to produce parts like trim and plastic sheet. The clinical field counts on extrusion for the manufacture of catheters, IV tubing, and other clinical tools. Even in food manufacturing, extrusion contributes in developing products like pasta or cereal. The stamina and adaptability of plastic extrusion, combined with its cost-effectiveness, make it an indispensable process across different sectors, check out this site underscoring its extensive practical applications.
The Future of Plastic Extrusion: Predictions and Trends
As we look to the horizon, it comes to be clear that plastic extrusion is poised for substantial advancements and improvement. Environmentally friendly choices to traditional plastic, such as bioplastics, are likewise expected to acquire grip. These trends suggest a vibrant, evolving future for plastic extrusion, driven by technical technology and a commitment to sustainability.
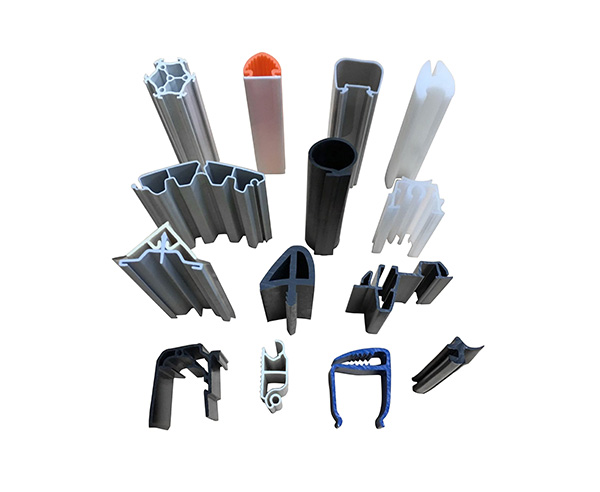
Conclusion
In verdict, plastic extrusion great post to read is an intricate procedure that makes use of innovative innovation and differed materials to produce diverse products. As plastic production proceeds to progress, it stays a necessary component of numerous industries worldwide.
In essence, plastic extrusion is a high-volume production procedure in which raw plastic product is melted and formed right into a continual account.While plastic extrusion is a typically used technique in production, the products used in this process substantially affect its final output. At its core, plastic extrusion entails changing raw plastic material into a continual profiled shape. It has led to the growth of sophisticated extrusion machinery, which has actually improved the efficiency and quality of the plastic extrusion procedure.In final thought, plastic extrusion is a complex procedure that uses innovative modern technology and varied products to produce varied items.
Report this page